Cleanrooms
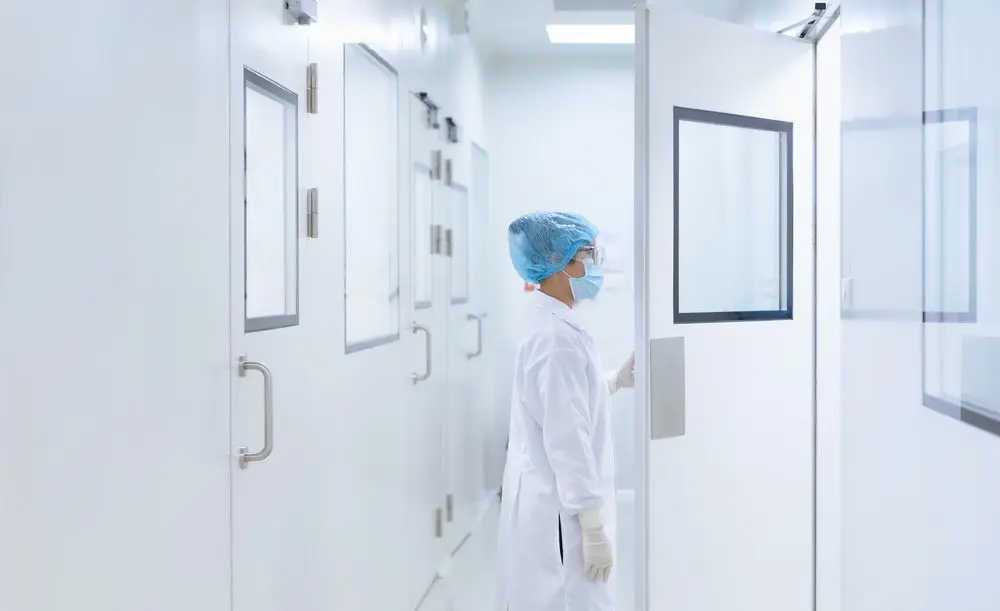
Cleanrooms are used in a wide variety of industries, from manufacturing and pharmaceuticals to biotech and aerospace. Similarly to cold rooms, they vary in size and complexity – but they can designed and built by MTCSS to suit the exact requirements of the industry and specification.
A cleanroom is a contained space which is designed to reduce contamination and to control other environmental parameters such as temperature, humidity and pressure.
What Defines A Cleanroom?
Cleanrooms are a type of temperature-controlled room which have specific classifications and requirements – they are designed to maintain a controlled environment with low levels of pollutants such as dust, airborne microbes, aerosol particles and chemical vapours. The air delivered to a cleanroom passes through HEPA filters, and in some cases where stringent cleanliness performance is necessary, Ultra Low Particulate Air (ULPA) filters are used.
A cleanroom has a controlled level of contamination specified by the number of particles per cubic meter at a specific particle size. They are classified by how clean the air is – in Federal Standard 209 (A to D) of the USA, the number of particles equal to and greater than 0.5μm is measured in one cubic foot of air, and this count is used to classify the cleanroom.
In the UK, BS EN ISO 14644-1 has recently superseded British Standard 5295 to classify cleanrooms.
The regulations and standards that a cleanroom needs to meet will be dependent on the application and the industry it is being used in. Depending on your industry and application, you might have to comply with an ISO 5 to 8 class standard (find out more about ISO classes here), the FDA and ISO-14644 regulations. For example, in pharmaceuticals you will certainly have to comply with GMP – our expert team will ensure your design complies with the specific regulations to achieve the certifications and validations required.
HVAC design in cleanrooms is not only driven by the cleanliness of the room, but also by the temperature required, the humidity and the pressure differential. These requirements are defined by the processes involved in the cleanroom and the comfort of the personnel working within the cleanroom.
The temperature and relative humidity of the room is a major factor in the design of HVAC for cleanrooms. During the design process, the heat produced by personnel and the equipment must be considered for it be compensated by the temperature control.
What We Need To Know To Design A Cleanroom
Designing a cleanroom has more moving parts than designing a ‘typical’ cold room, so the information that we need to create a cleanroom to your requirements is more detailed.
The level of cleanliness in your cleanroom will determine the ISO class required for your rooms. These classes are sometimes enforced by a guideline (such as USP, GMP, FDA) – or they can be defined by your company’s internal quality policy. Cleanrooms at ISO 8 and above also require an airlock.
To decipher the exact design to suit your requirements, our team will work with you to answer a range of questions…
• What size cleanroom is required?
• What are your door and window requirements?
• Do you require any antechambers / gowning rooms / airlocks?
• Do you need any washing stations.
• What level of cleanliness do you need?
• What are the processes that will take place inside the cleanroom?
• What ISO class must your cleanroom adhere to?
• Are there any other specific regulations & standards that need to be adhered to?
• Are you using any specific chemicals / solutions / solvents?
• The required temperature – including the setpoint and tolerance
• The humidity and pressure differential
• What is the ambient temperature in the space the cleanroom will be built?
• How many people will be working in the cleanroom
• The equipment in use
• The heat any equipment generates
If you are unsure about any of the questions above, one of our team would be happy to discuss your project and requirements in detail. Call us on 01886 833381, email us at sales@mtcss.flywheelsites.com or fill in an enquiry form here.
Compounding Chambers
Compounding chambers are a form of cleanroom utilised for sterile compounding pharmacies – compounding chambers are where the process of mixing drugs takes place in strictly controlled (temperature & humidity) cleanroom.
There are three main factors that determine the regulations that apply to a compounding facility: the type of preparations being compounded, the geographic market the facility operates within and the geographic market the compounded preparations will be sold.
The HVAC systems utilised within compounding chambers is vital, from the pressure and humidity control to the temperature control and air conditioning systems. Air conditioning and humidity are a key element to ensure the comfort and safety of personnel working within the compounding chamber.
When designing a compounding chamber we need to consider:
• The type of products being compounded – non-hazardous sterile compounding preparations; hazardous sterile compounding preparations; hazardous non-sterile compounding preparations; non-hazardous non-sterile compounding preparations
• The regulations required – USP-797; USP-800; ISO 14644-1:2015; NAPRA
• These regulations are dependent on the pharmacy regulatory authority of the location the facility is located and where the compounded preparations are sold
• Other considerations to take place are similar to that of cleanrooms (as listed above)
Our expert team can discuss your requirements regarding layout (including buffer zones, PEC, anterooms and AHU), HVAC systems and adhering to specific regulations. Get in touch with MTCSS by calling us 01886 833381, emailing us at sales@mtcss.flywheelsites.com or fill in an enquiry form here.
Frequently Asked Questions
Cleanrooms are classified by the number of particles per cubic meter at a specific particle size – essentially, they are classified by how clean the air is. In the UK, the classification is by BS EN ISO 14644-1, which is the compliance with ISO 1 to 8. However, there are other cleanrooms classifications to consider dependent on your country, industry, and application. Pharmaceutical cleanrooms may need to comply with other specific regulations, certifications and validations.
Cleanrooms are utilised in a wide range of industries that require the adherence to a specific range of classification in relation to air cleanliness. They are commonly used in pharmaceuticals, biotech, and aerospace, but are also used for a range of other applications.
Compounding chambers are a type of a cleanroom that are used in sterile compounding pharmacies – essentially where the process of mixing drugs take place.
The key element to understand when it comes to designing a cleanroom is the classification required. This is because it effects the design of the cleanroom and the HVAC systems. But here are some questions to consider when designing a cleanroom:
The level of cleanliness required
The ISO classification and other guidelines for the cleanroom to adhere to
Size of the cleanroom and any other adjoining rooms eg. antechambers and gowning rooms
Access requirements and cleanroom doors / access points
Humidity, temperature, and pressure requirements
The processes taking place within the cleanroom and the personnel
Cleanroom design can be a complex process, but our team are here to help you understand the process and design a cleanroom for your requirements.
Related Projects